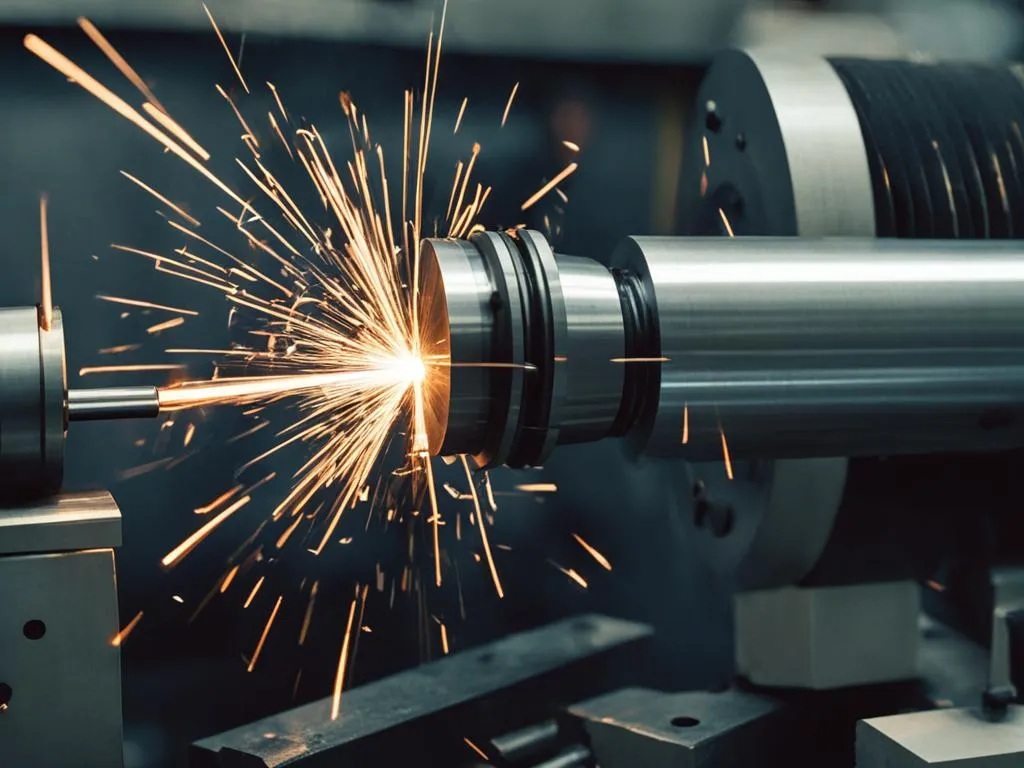
Shaft Machining Customizations: Process Tips and Methods

The shaft machining technique is an effective way of producing long and cylindrical mechanical components of engines that convey power and torque within equipment. Furthermore, these precise shafts come in a variety of forms and are essential components used in a wide range of applications and sectors, from construction to industrial machines.
However, it is critical to grasp everything about shaft machining since each machined shaft must meet the exact requirements of the intended use. This article will define a machined shaft and explain how to process custom machined shafts. You will also learn the procedures and factors for efficient shaft machining.
What Is a Machined Shaft?
A machined shaft is a cylindrical or round mechanical component that transmits rotational motion and power between machine components. These machined shafts are commonly constructed of metals such as aluminum, titanium, steel, or stainless steel, depending on the specifications of the intended application.
These shaft pieces play a key role in conveying rotational force and torque within machines, allowing for more efficient and smooth operation. Furthermore, a custom-made shaft can improve the performance and functionality of a machine in its intended uses.

How Are Custom Machined Shafts Processed?
Custom shaft production entails a variety of steps that contribute to the desired diameter, accuracy, and surface polish. To design functional custom shafts, it is important to first define the desired use, operating circumstances, and project requirements. Here are the processes for processing custom machined shafts.
Program and Designing
The first step in creating custom-machined shafts is to design and program. You must decide the shaft's material, diameter, and length. The CAD (computer-aided design) file for your custom-machined shaft will then be created using CAD software.
Then, using computer-aided manufacturing (CAM) software, create tool paths for the CNC machine based on the shaft components' specifications. To accomplish this, use CAM software to create a CNC program (a collection of machine-readable instructions known as G-code). After that, you'll feed it into the CNC machine controller to direct the milling operation.
Setting Up the Machine
When setting up a CNC machine to produce shafts, you must select the right machine type, such as a milling machine or a lathe. Then, prepare the workpiece and select the appropriate cutting tool, such as end mills or turning tools. Also, utilize sharp cutting tools and secure the workpiece tightly with the proper fittings.

Shaft Machine Process
It is preferable to utilize CNC equipment to cut the custom shafts to the desired specifications. Machinists frequently use the CNC turning process because of its versatility and high precision in cutting cylindrical components like custom shafts. It spins the cylindrical shaft as the cutter removes material. However, quality assurance requires monitoring the machining phases and inspecting the machined shafts.
Finish the Surface
Following the manufacture of your bespoke shafts, you may pick from a broad range of appropriate surface finishes. These surface treatments may be used to improve the functionality and look of machined shafts, ensuring that they meet the criteria of the intended application. Bead blasting, anodizing, and passivation are all examples of acceptable surface finishes for custom shafts.
Different Kinds of Machined Shafts and Their Purpose
Hollow Shafts
Hollow shafts frequently have a center hole or void through which fluid, cable, and other components can travel. They are generally lighter than solid shafts of the same size. Hollow shafts are used in racing cars and airplanes to minimize weight. They also apply to conveyor systems, pumps, and medical devices.
Threaded Shafts
These machined shafts feature internal or exterior threads that match the threads on the appropriate item, such as a nut. This type of connection is commonly used in applications that need repeated attachment or removal, such as electrical or plumbing work. Threaded shafts are also utilized in threaded spindles, lead screws, and fastening systems.
Keyed Shafts
A keyed shaft is a machined shaft that has a keyway cut into it to hold components like sprockets, pulleys, or gears. The machined keyways are the same width as keys. As a result, the keyway accommodates the key by gripping the opposite component's equivalent teeth, preventing it from spinning independently or sliding. Keyed shafts are useful for connecting high-torque components such as motors and pumps.
Splined Shafts
These machined shafts have longitudinal grooves or splines cut into them that match the splines machined into a corresponding component, such as a pulley or gear. This is a robust connection that allows for continuous power transfer since there is no relative movement between the two sections. They are commonly used in applications requiring precision positioning or torque transmission, such as automobile transmissions and gear couplings.
Tapered Shafts
A tapered shaft gradually reduces in diameter throughout its length. Tapered shafts are commonly employed in applications that need tight mounting of components such as automobile wheel hubs, pulleys, or gears.
Methods Used to Manufacture Precision Shafts
Manufacturers frequently use a variety of procedures when machining precision shafts to obtain desired tolerances and surface finishes. Here are some popular shaft manufacturing procedures.

CNC Turning
This procedure is perfect for turning cylindrical items, such as precise shafts. The CNC machine rotates the shaft attached to the chuck while the cutting tool eliminates extra material from its surface. CNC turning achieves the necessary diameter and surface quality for machined shafts. More significantly, CNC turning is the preferred method for high-volume manufacturing when a large number of shafts must be produced fast.

CNC Milling
Milling is a fast procedure for cutting a blank with revolving cutters to create features like splines, flats, and keyways on the surface of precision shafts. The fixed shaft is chopped into the necessary shapes and sizes using spinning multi-point cutters.

CNC Grinding
Precision CNC grinding is a machining method that uses an abrasive spinning wheel to smooth the surface of machined shafts, ensuring that they fit the desired dimensions and tolerances. This procedure is similar to CNC machining; however it does not employ a cutting tool. A rotating grinding wheel contacts the shaft's surface to shape it.
CNC Drilling
The CNC drilling method creates holes and channels across precise shafts, allowing gears to attach to them. This process produces grooves with various diameters and depths, allowing the machined shaft to work properly. Drilling is less costly and simpler than other approaches.
Electrical Discharge Machining
Electrical discharge machining (EDM) is an aided technology for cutting precise shafts. It employs electricity to vaporize the workpiece blank before cutting it. EDM is used to cut minute features from metal materials. Furthermore, EDM is an effective technique for creating fine details in solid machined shafts.
What Materials Can We Use for Machining Shaft Parts?
Precision shafts can be machined from a variety of materials depending on the purpose. These materials must have exceptional strength and endurance to meet the demands of the intended use. Common types of suitable materials are:
Aluminum
Aluminum is a light, corrosion-resistant material. It has great machinability, making it ideal for a variety of applications where weight is critical. If your application demands lightweight machined shafts, aluminum is the material to choose.
Stainless Steel
Stainless steel is a dependable metal for producing precise shafts. When corrosion resistance is critical, product engineers frequently turn to stainless steel. For example, stainless steel grades 304 and 316 provide good corrosion resistance. As a result, they are widely used in applications that need frequent exposure to water or corrosive components, such as chemical processing facilities or coastal settings.
Carbon Steel
Carbon steel provides exceptional tensile strength and machinability. It can endure thermal treatments to increase its hardness. As a result, it is a frequently utilized material in shaft machining. The 1045 grade is a good example of a carbon steel material with moderate strength that may be used for pump or motor shafts.
Titanium
Titanium is a popular material for machining precise shafts for high-performance applications because of its high strength-to-weight ratio and excellent corrosion resistance. Titanium's characteristics make it popular in the aerospace industry for precise shafts.
Alloy Steel
It provides the high strength and hardness needed in precisely machined shafts. Alloy steel 4140 or 4340 are common alloys used to manufacture precise shafts for heavy-duty applications such as equipment and big industrial motors.
Nickel Alloys
Nickel alloys are suitable for machining shafts in high-demand applications. It has outstanding corrosion resistance and high-temperature strength. Inconel is a nickel alloy that is well-suited for precision shafts in turbines and other high-temperature applications.
Surface Finish Options for Customized Machined Shafts
Surface treatments are effective at improving performance, durability, hardness, corrosion resistance, and wear resistance for custom shafts, depending on their intended purpose.
Passivation
Custom shaft passivation improves the surface of stainless steel shafts. It entails washing the surface of the machined shaft with an acid solution to remove free iron compounds and other impurities. As a result, a passive oxide layer develops on the shaft's surface, increasing its resistance to corrosive substances.

Anodizing
Anodizing is best suited for aluminum machined shafts. It generates a strong, corrosion-resistant coating on the surface of the machined shaft, improving both its aesthetics and corrosion resistance. Anodized shafts take a variety of color dyes for ornamental uses.
Electroplating
Electroplating is a dependable surface treatment that improves the surface of machined shafts by depositing a small layer of metal such as zinc, nickel, or gold on them. This surface treatment increases wear and corrosion resistance.
Bead Blasting
Bead blasting is a great surface finish that entails releasing steel beads or fine glass under high pressure to polish the surface of your machined shafts. The bead blast finish provides your custom shafts a smooth surface with a dull or satin appearance.
Polishing
Polishing is a surface finishing technique that protects machined shafts from contaminants and oxidation. It employs an abrasive substance to remove nicks and scratches from the surface of your custom shafts, increasing corrosion resistance and reflecting characteristics.
What To Keep in Mind When Manufacturing Shaft Parts
Certain aspects must be considered when making shaft components. Here are some important factors for good shaft component fabrication.
Expected Load and Torque
It is critical to determine the predicted stress and torque that the machined shaft will experience in your intended application. It contributes to the production of dependable and precise shaft components, hence preventing shaft failure. Most importantly, it can determine the best material and diameter for making durable and functioning shaft components.
Shaft Material
Material strength, temperature, and corrosion resistance are all important considerations when selecting a material for shaft components. It helps to guarantee that the machined shaft and parts survive a long time and work well in their intended use.
Furthermore, the selected material must be able to sustain the application's loads without failure. Furthermore, each machining material has benefits and downsides. Choose the one that best fits your project's needs and budget.

What Is a Shaft Length and Diameter?
To minimize errors like as deflection and excessive vibrations, machine the shaft and its components to the required length and diameter for your planned uses. More significantly, it would be beneficial to select a cross-sectional form that can adequately sustain the loads that the shafts would be subjected to.
Finished Surface
Adopting a proper surface treatment for your machined shafts is critical to ensuring their lifetime. There are several surface treatments that are suitable with different types of shafts. Shaft components that have been anodized, powder coated, or passivated are more resistant to corrosion, wear and friction.
Shaft Machining Quality Control
Ensuring quality control is critical for producing functioning machined shafts. Regular quality inspections guarantee that the machined shaft's dimensions, material qualities, and surface polish meet the specifications. As a result, you may use processes like surface roughness testing, coordinate measurement, and hardness testing during quality control.
Furthermore, continuous quality checks enable rapid identification and rectification of any faults, reducing waste and guaranteeing that the machined shaft fulfills the desired requirements.
For more information on our Mitsubishi servo drives, motors, and systems, as well as drives, motors, and systems from other leading manufacturers, as well as other parts and components for your equipment and machines, please call CNC Tools Industrial Electronics at (956) 246-7411.
One of our knowledgeable customer service representatives can prepare a parts and components quote for everything you need for your equipment and machines, as well as help, arrange maintenance, repair, or installation service from one of our experienced technicians.