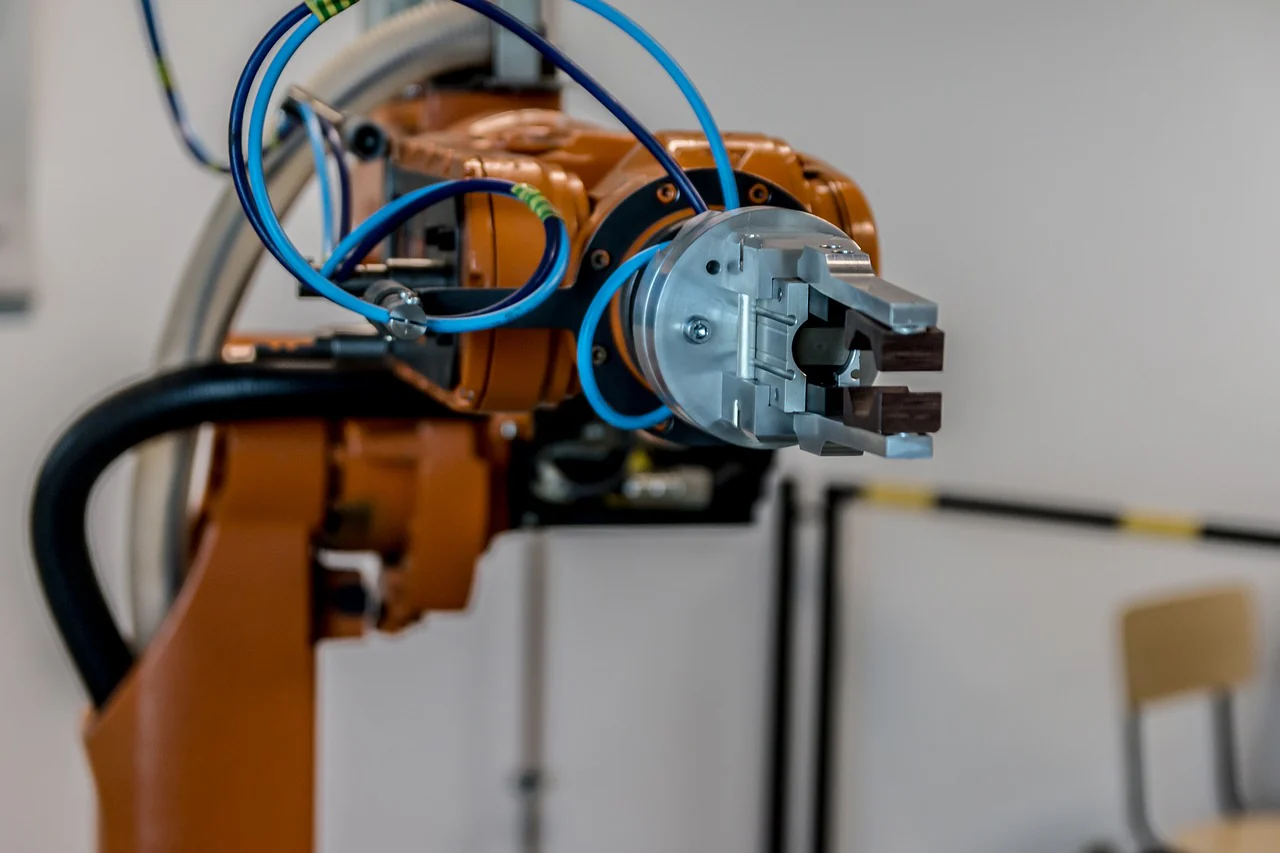
Selecting Your Encoder
What does an encoder do?
Any motion control method needs a sensing device to deliver accurate feedback sensing in order to function. The component of the equipment that provides feedback data is the encoder.
How is the encoder put to use?
A motion signal is received by the encoder, which then transforms it into an electrical signal that can be read by a PLC or other motion control system. The signal is then used by the motion control system to regulate aspects of your machines including speed, direction, and position. Any application can use this procedure: The precise performance function is produced by the information exchange between the machine and the controller via encoder signaling.

Selection Criteria:
What should you consider while selecting the best encoder for your application?
There are a few key considerations when choosing the right encoder for the task. The application control requirements are one thing you must decide before choosing an encoder. Applications might be for extremely basic machines or sophisticated equipment. Some applications are straightforward and need for low-accuracy position or speed control, whereas more complex machines could call for a greater level of feedback. During the selection phase, it is essential to understand the encoder's application.
The encoder characteristics are something else to consider. This usually refers to the number of rectangular pulses per motor rotation. Two channels provide a pulse number. The two channels, commonly referred to as quad counts, have a quarter-pulse-length phase shift. In this method, the four unique states of each pulse may be used to determine the direction of the motor. The true resolution is represented by these four pulses. For instance, if an encoder has 2,000 counts each pulse term, it offers 8,000 states every turn, which establishes a nominal resolution of 360/8000=0.045°. Encoders may identify motion at a variety of counts per turn. Therefore, you must choose if your application calls for a straightforward encoder with fewer CPT or a sophisticated encoder that can detect a position or speed with a high degree of accuracy.
Other elements may affect resolution. The mechanical layout, in addition to other factors like analog or digital signals, is taken into account while determining encoder resolution. Encoder resolution may also be influenced by underlying physical concepts like magnetic, optical, or inductive principles.
Exposure to environmental variables is also considered when making a decision. If the encoder is going to be exposed to elements like dampness, dust, or chemicals that might corrode metals, it could need protection. Extreme environmental factors like temperature, stress, or vibration can damage encoders.
Types of Encoders:
Identifying the sort of movement, the encoder is detecting is a straightforward way to help you decide about encoder possibilities. Linear, rotary, and angle encoders are the three types of encoders most frequently employed.
The linear encoder is a type of encoder that records location by detecting the movement of linear objects. It is decided on a scale that enables the sensor to translate the encoded location into an analog or digital signal. A motion control system may then decode the signal into a position. The linear encoder is used by machining tools to coordinate measurement equipment, such as a cut length application. When using a cut-length application, the control device and encoder decide how much of a certain item, like fabric, is sent through the machinery, calculating where to cut. An encoder and a moving item may occasionally be connected by a cable. A transducer is then used to provide an analog or digital output signal that may be used to determine the movement or location of the object.
A rotary encoder is used for spinning items. A rotary encoder translates the angular position of the moving shaft into an analog or digital output signal, giving feedback on the movement of a spinning item or equipment. The position or speed of the shaft can be determined by a control system using this signal. Rotary encoders, also known as shaft encoders, can be fitted directly to any spinning shaft of machinery, including motors. The absolute and incremental rotary encoders are the two primary varieties. What sets these two apart from one another? It's the output that differs.
While the incremental encoder offers details about the motion of the shaft, the absolute encoder displays the present shaft position. The incremental encoder normally handles data like speed, position, and distance, whereas the absolute encoder is an angle transducer. Robotics and industrial controls are two examples of applications for the rotary encoder that call for monitoring and/or control.
Similar to rotary encoders, angle encoders are more likely to provide greater precision. It calculates a spinning shaft's angle of rotation. An optoelectric sensor on the stator and an optical grating are used in a disc-shaped rotator. An angle encoder is employed to maintain the rotor and stator in a concentric position utilizing bearings because optical technology depends on the tightly limited rotation of the rotor in respect to a stator.
If you need assistance in finding the drive, motor, or servo system you require, just let us know. We have access to a worldwide supply chain network and can locate exactly what you need. We also offer a wide range of other parts and components for a variety of machines and equipment, including:
- Spindle Drives
- Spindle Drive Motors
- Monitors
- Controls
- Circuit Boards
- Power Supplies
- Rotary Tables
- Other Motors
Our qualified customer service representatives can help assist you in locating parts for your machines and equipment, provide you with a quote, and help you set up maintenance, repair, or installation services from one of our qualified technicians. To further demonstrate that you are aware of what to look for, contact us at (956) 246-7411 or send an email to services@cnctoolsllc.com if you need any further assistance